Breakdowns and malfunctions are routine hazards in any industry that uses conveyor belts. The consequences of a disrupted conveyor belt system can be severe, from downtime and lost revenue to safety risks and decreased production efficiency. Implementing a comprehensive maintenance plan is essential to ensure your operation stays on track, literally and figuratively. Here’s the ultimate checklist for conveyor belt maintenance. It’ll help you keep your belts running smoothly and your business moving forward.
Routine Visual Inspections
Routine visual checks are the frontline defense in the battle against conveyor malfunctions. Each day, before starting operations, take a walk along the belt's path and visually inspect the entire system. Look for any anomalies, from tears and splice failures to material buildup and belt sag. Check side skirts, chutes, dust curtains, and the area surrounding the conveyor to ensure they aren’t interfering with the belt's operation.
This daily survey will often catch potential problems at their inception, allowing you to act before they become emergency shutdowns. Establish a clear protocol and log these daily findings to observe patterns over time.
Belt Tension and Alignment
The proper tension and alignment of the belt are fundamental to its function. A lopsided or deflated belt can lead to material spillage, increased friction, and accelerated wear. Tension gauges should become familiar to your maintenance crew, as they must consistently maintain correct tension levels.
You should address misalignment, detected through sighting along the belt from the head and tail pulleys, promptly. Correction may involve simple adjustments or more complex realignments, but ignoring these issues can lead to disastrous consequences.
Lubrication of Moving Parts
Lubrication of moving parts is another critical aspect of maintaining an efficient and safe conveyor belt system. Proper lubrication reduces friction between moving components, minimizing wear and extending these parts’ lifespan. Regularly inspect all dust seals and wiper blades, and keep moving parts greased.
Remember that over-lubrication can be just as harmful as under-lubrication. Each type of conveyor system will have different prerequisites for lubricants and application methods. Referring to the manufacturer's guidelines is essential to ensure your specific belting, such as modular plastic belting, remains in peak condition.
Cleanliness Check
The cleanliness of your conveyor system directly impacts its efficiency. Dirt can reduce belt traction and lead to slippage, which causes backpressure on the pulleys, overloading the motors and ultimately leading to tracking issues and premature wear.
Simple, periodic cleaning with the right tools and techniques can prevent these problems. Establish a cleaning schedule, train your staff in proper cleaning methods, and use suitable cleaning agents that won’t degrade the belt surface.
Roller and Pulley Checks
Rollers and pulleys do a strenuous job of supporting the entire weight of the conveyed material. Regularly inspect each roller for any sign of damage or misalignment. They should rotate freely without any noise or obstruction.
You should remove dirt or spilled material that has collected on pulleys. Damaged rollers or pulleys can cause the belt to drift or become misaligned, so prompt replacement or repair is vital. This system operates in synergy; one faulty roller affects the entire operation.
Electrical and Control Systems Inspection
In modern manufacturing, the electrical and control systems are the brains behind your conveyor's operations. Yet, they can also be a point of failure if you don’t properly maintain them. Ensure all electrical connections are secure and free of corrosion.
Check for wear or damage to the wiring and conduits. The control panel should be clean and free of overheating or abnormal noise. Regular testing of control systems, including emergency stops, is also crucial. Note that modifying these systems requires professional knowledge, and you must document changes well.
Review of Belt Splices
People often overlook the integrity of the belt splice until it fails. However, reviewing belt splices should be a routine part of your maintenance checklist. Check for wear and damage, and inspect that splice plates and fasteners are secure and undamaged.
Splice areas should be free of product residue, which can interfere with the belt’s operation. If you find any sign of splice compromise, don’t delay addressing the issue. Ensuring the structural integrity of the conveyor belt is crucial to preventing any mid-operation split that could damage goods or pose a danger.
Verifying Function of Safety Measures
This is more than a maintenance point; it's a life-saving measure. Ensure all safety guards and devices are in place and functional. Investigate any incidence of safety-feature activation to ensure it wasn't an indicator of a larger problem with the conveyor system.
Periodically run emergency drills to ensure your team knows the safety protocols by heart. Also, evaluate the safety signage. It should be visible, and all personnel should understand it. Regularly workshop your safety measures to ensure you’re taking the best precautions.
Periodic Audits
Conducting a periodic, comprehensive audit goes beyond daily visual checks. Audits should involve detailed inspections from a trained, competent person who understands the intricacies of your particular conveyor system. These detailed checks can rectify any oversights in the more routine visual inspections. Consider the time and expertise needed for such audits. Also, plan them into your maintenance schedule according to the conveyor's usage and age.
Replacing Parts As Soon as Possible
Proactively replacing worn or damaged parts is crucial for maintaining conveyor belt system efficiency and safety. An inventory of replacement parts isn’t just a backup plan. It's a key part of a well-organized maintenance strategy. Having these components on hand can significantly reduce downtime due to breakdowns, enabling immediate repairs.
Delaying the replacement of failing components not only affects your system's operation but also risks safety and leads to costly repairs later. Swift action is vital in the dynamic conveyor environment where every minute of downtime means lost revenue. Establishing a reliable inventory of essential parts and replacing them at the first sign of wear or damage is an investment in system reliability and workplace safety.
Employee Training
Your conveyor system is only as effective as those operating and maintaining it. Training your employees mitigates the risk of accidents and ensures that the daily operations don't unknowingly cause malfunctions or wear. Create a robust training program that covers the basic principles of conveyor systems, their specific maintenance requirements, and the correct reporting procedures for defects.
By adhering to our ultimate checklist for conveyor belt maintenance, you're performing due diligence and safeguarding your facility's efficient operation and the well-being of your workforce. It's time to integrate this checklist into your daily practices.
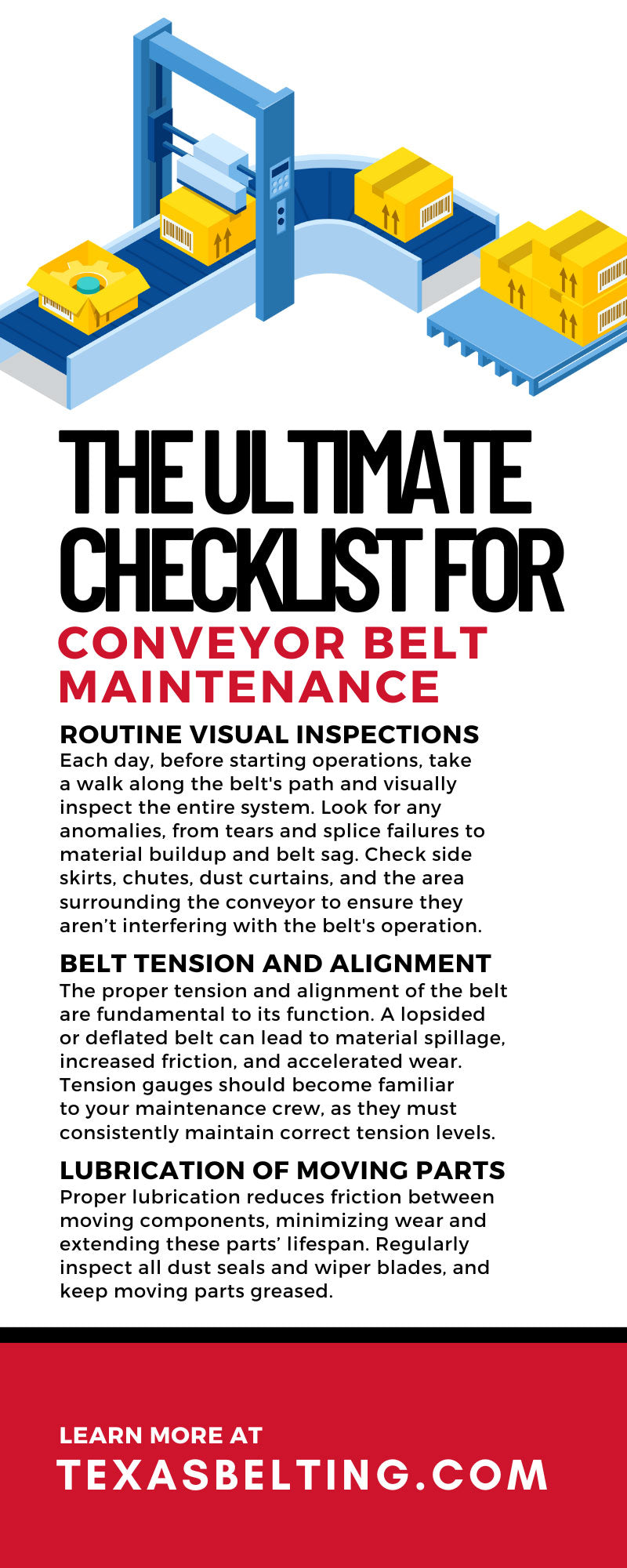