Whether you work for the food industry or construction, no matter the type of trade your warehouse operates under, running your conveyor system optimally plays a crucial part in your business' success. Convery belt systems run the show for many warehouses. They transport goods from one location to another and through various assembly lines. One mishap with the conveyor belt leads to numerous issues and even risks halting production altogether. Ensuring your conveyor belt system operates to its full potential minimizes any productivity losses, reduces safety risks, and maintains the quality and functionality of operations. Here are seven tips for optimizing your conveyor belt systems and keeping your business running smoothly.
Conduct Regular Performance Checks
Conveyor belts handle various precious products, from produce to large equipment like car parts. Conducting regular performance checks ensures your handled goods remain in safe hands. It also brings to light any malfunctions. Figuring out any issues on a test run minimizes future risks of halted production lines and damaged goods during actual runs. While performing a test run, try to imitate actual operations using test carry items in similar sizes, shapes, and weights. Some common concerns to look out for include:
- Mistracking
- Belt slippage
- Inaccurate speed times
- Loose bolts and screws
- End of the line damages to test product
- Rattling or buzzing sounds
- Unusual wear and tear
- Sudden system shutdowns
Conveyor systems include a wide range of parts: pulleys, rollers, belts, and other systematic add-ons for productions. Regular test runs and performance checks ensure all of the conveyor's moving parts are still whole and operating at all times.
Choose the Right Belt for Your Needs
Depending on your conveyor's purpose, industry, and handling items, the most beneficial belt for your needs varies. Belting suppliers offer a wide variety of belt materials to choose from. The most common material forms include rubber, polyurethane, and PVC. Each belt type offers varying properties that aid and benefit certain scenarios and manufacturing sites. Certain conveyor bands like PVC belts are also recognized and approved by industry-qualified organizations, such as the FDA.
Different belts possess different properties relating to resistance, grip, elasticity, temperature compatibility, speeds, durability, longevity, maintenance, and care. Some belt materials come reinforced with fiberglass, nylon, and thermodynamic plastics and polymers, further enhancing their properties and abilities. Choosing the right belt for your needs optimizes your system to meet your industry's standards and processes.
Replace Worn-Out or Damaged Parts
Since conveyor belts play a crucial role in the productivity of a warehouse, they undergo consistent and intense strain for long periods. Over time, the constant pressure and use of the belts lead to significant wear, minimizing the quality and functionality of the belt. Worn carcasses, tears, and lost elasticity often occur as the belts reach the end of their lifeline. Any belt degradation affects the belt's performance and the efficiency of your work.
Replacing belts and other worn conveyor parts maintains optimal production and reduce risks of potential errors and further damage to your system. Similarly, switching out damaged belts and conveyor equipment minimizes future mishaps, stopped productions, and safety hazards.
Tend to Maintenance Issues Immediately
Errors are bound to occur with any large system. With the various moving parts of a conveyor belt, numerous malfunctions can arise from colliding carried products to carryback. Tending to maintenance issues immediately prevents any domino effects of mishaps and potential future damages. The longer you wait to fix certain concerns, the more effect they have, and the more likely they will influence your performance. Knowing common conveyor issues helps you know what to look out for and when potential maintenance might need to intervene.
Clean Your Equipment Regularly
Conveyor systems rely on movement to operate. Anything hindering its various moving parts affects the functionality of the belt and your warehouse's productivity. Many potential influences create possible barriers affecting your conveyor's functionality, like sticky residue spreading, sticking, and blocking rollers and pulley parts.
Debris and dirt also cause lots of concerns when built up, causing uneven wear and tear, misalignment, and damage to the belt and carried products. Plus, they cause various safety risks and health hazards in certain worksites. Cleaning your equipment regular ensures no debris, residue, dirt, or carryback hinders the mechanism of your conveyor and efficiency.
Implement and Establish Conveyor Safety
Optimized systems not only cover productivity and performance quality. It also refers to safety. When conveyor belts function at their max potential, they provide high standard results, minimizing various malfunctions and issues, running efficiently, and producing minimal to no health and safety hazards. Implementing and establishing conveyor safety keeps dangers away, minimizing the need to stop work to tend to accidents.
One of the most effective ways to enforce conveyor safety is through adequate employee training. Teaching every staff member proper safety protocols and the risks on their worksite ensures everyone makes an effort to enact and comply with the same safety procedures, preventing chances of risks. Plus, training educates the workers on proper equipment handling. Safety standards to sanction include:
- Dresscode: no loose clothing items, hair, and jewelry
- No running, sitting, or standing on moving conveyor belts
- Ensure someone is watching the system at all times
- Avoid potential pinch spots
- Clear the belt's surrounding area
- Only allow authorized personnel to operate systems
- Wear safety gear: hard hats, gloves, closed-toe shoes
- Do not remove and check conveyor guards
Safety standards reduce risks, optimize systems, and improve productivity.
Operate With the Ideal System Settings for Your Equipment
Akin to choosing the right belt material for your needs, operating with the ideal system settings ensures your equipment's success. Certain conveyor uses require specific setting mechanics to operate and function optimally. Printing and packaging systems benefit from running at high speeds. Meanwhile, handling valuables benefit from operating at slower speeds. Conveyor systems equipped with polyurethane belts can withstand high temperatures, while rubber belts can't. Also, some systems are compatible with inclinations. Depending on your equipment and process, the way you operate your system can vary.
There are many ways to optimize a system to best fit your needs, from regular check-ups to specific operational procedures. Optimizing your conveyor belt systems maintains your warehouse's quality, efficiency, and productivity. It also ensures the safety of your workers and handled items. With an optimized system, you can reap all the benefits of a conveyor belt, and more.
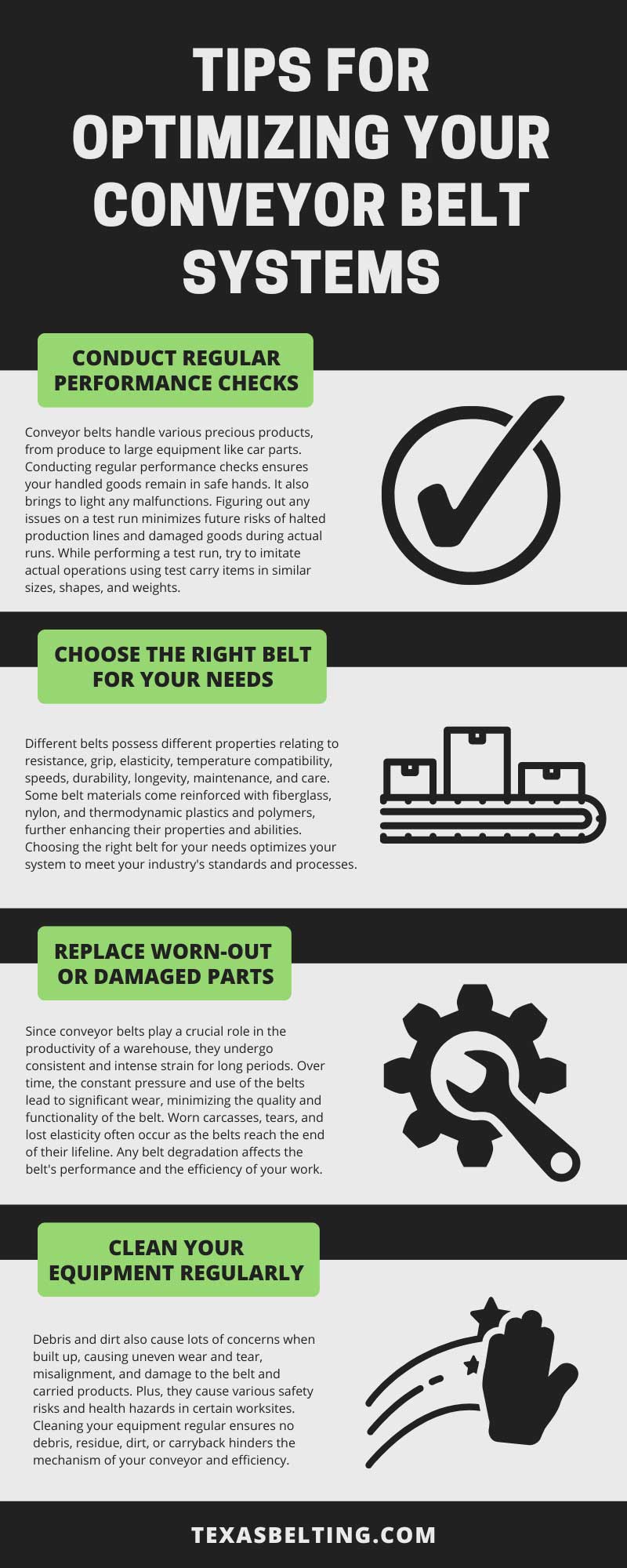